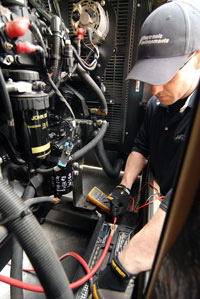
Today’s facility managers need to evaluate incident response procedures and plan ahead for regular maintenance. Generator failures like these happen more often than they need to. Understanding the following issues can reduce your odds of a failure. Here is what you need to know.
1. Battery Maintenance
Emergency power systems specify batteries that must be assured of starting power. Type, construction, chemistry and classification must meet expectations. Another common cause of battery performance failure is improper adjustment and operation of the battery charger, often with loose or dirty cable connections due to corrosion.
2. Wet Stacking
Diesel engines are designed to operate at a particular temperature. Running a generator for long periods of time at less than optimum temperature can cause the engine to over fuel and leak, potentially causing damage. An automatic load bank can help to prevent such a failure if utilizing the building load is not an option.
3. Fuel Contamination
Good fuel quality is critical and often neglected. Fuel can become stagnant, stale, and contain excess water. Sediments can build up in the tanks bottom risking damage to the generator and contaminating new fuel. Testing and cleaning fuel as part of scheduled maintenance assures proper operation.
4. Incorrect Switches and Breakers Position
Not in auto, a human error! Maintenance routines often neglect to restore controls to a proper ready position after service is performed.
5. Dirty filters: air and fuel
Emissions systems require strict filtration and add the side effect of making generators more susceptible to the environment they are in. Older generators typically suffer with the high additive and low sulfur of today’s diesel fuel adding to the clogging of fuel lines or filters by cleaning out material in the system.